I’ve been stripping back the wire cover all the way so only bare wire is being crimped in, then I solder it. I just watched a video where the person only stripped enough to be crimped in the top set of crimp tabs. The bottom crimp tabs were crimped around the wire covering. Is that the preferred method or is the way I’ve been doing it ok?
Nothing has failed on me and I never leave exposed wire or connectors. This is before soldering.
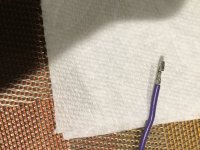
Nothing has failed on me and I never leave exposed wire or connectors. This is before soldering.
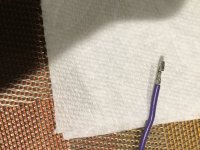
This shows a good photo, but read the entire article.
https://www.hughshandbuilt.com/2016/07/29/how-to-properly-crimp-wires-and-terminals/
https://www.hughshandbuilt.com/2016/07/29/how-to-properly-crimp-wires-and-terminals/
Experienced people say crimp OR solder the wire to the lug / pin / whatever..
Both methods have their pros and cons.
In cars, the harness systems are made on automated lines, wire is cut to length, stripped and crimped. Those have to last long in harsh conditions, so a lot of experience goes into their manufacture.
The idea of gripping insulation in the away set of tabs is that the wire is not pulled, and the joint not disturbed, if somebody jerks it around, unlikely in audio, quite likely in a car.
Please read the article mentioned above to get a better idea of what I am trying to convey.
And if you do need it a lot, a high quality crimping tool is a wise investment.
Both methods have their pros and cons.
In cars, the harness systems are made on automated lines, wire is cut to length, stripped and crimped. Those have to last long in harsh conditions, so a lot of experience goes into their manufacture.
The idea of gripping insulation in the away set of tabs is that the wire is not pulled, and the joint not disturbed, if somebody jerks it around, unlikely in audio, quite likely in a car.
Please read the article mentioned above to get a better idea of what I am trying to convey.
And if you do need it a lot, a high quality crimping tool is a wise investment.
Properly made crimps are more reliable than soldered, and have better strain-relief. The pressure generated by the crimp tool cold-welds the crimp to the wire, cutting through any oxide layer in the process. If you don't have the correct crimp tool this superiority isn't guaranteed.
It all depends if the terminal crimp has just one set of "wings" for the stripped bare wire, or it has two sets of "wings" with the additional set being for over the insulation.
As for solder or not...Most of the time I don't, & it depends on the wire thickness & quality. However, when I want to make a 100% best connection I tin the wire, crimp the terminal over & then place the soldering iron tip on the terminal (crimped section) to melt the solder on the tinned wire. I also feed a bit more solder into the terminal. Then place heat-shrink over the terminal (you might have to slide the heat-shrink onto the wire before you crimp the terminal).
Photo below from when I rebuilt my speakers. The terminal on the left has 2 sets of wings & the wire was tinned & crimped, but not re-soldered. The terminal on the right has only one set of wings & the tinned wire has been re-soldered after crimping. Both have clear heat-shrink, & have been I.D. marked with white tape & a "Sharpie" pen.
I originally made all the speakers internal cables as per the left terminal, but later remade them all as per the right terminal. This to remove extraneous metal from the signal path & to provide a much better electrical connection. The cable terminals are not under any pull "stress", so additional "wings" (strain relief) around the insulation are not required.
For reference, both the cables are silicone insulated, 1000V, “test/measurement” OFC multi-strand wire called “Silivolt-1V” made by MC/Staubli as its highly flexible & soldering iron resistant. The left cable is the 0.75mm CSA version, & the right being their 2.5mm CSA version. The eye is for a M4 bolt/stud connection.
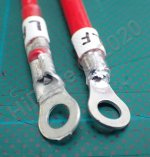
As for solder or not...Most of the time I don't, & it depends on the wire thickness & quality. However, when I want to make a 100% best connection I tin the wire, crimp the terminal over & then place the soldering iron tip on the terminal (crimped section) to melt the solder on the tinned wire. I also feed a bit more solder into the terminal. Then place heat-shrink over the terminal (you might have to slide the heat-shrink onto the wire before you crimp the terminal).
Photo below from when I rebuilt my speakers. The terminal on the left has 2 sets of wings & the wire was tinned & crimped, but not re-soldered. The terminal on the right has only one set of wings & the tinned wire has been re-soldered after crimping. Both have clear heat-shrink, & have been I.D. marked with white tape & a "Sharpie" pen.
I originally made all the speakers internal cables as per the left terminal, but later remade them all as per the right terminal. This to remove extraneous metal from the signal path & to provide a much better electrical connection. The cable terminals are not under any pull "stress", so additional "wings" (strain relief) around the insulation are not required.
For reference, both the cables are silicone insulated, 1000V, “test/measurement” OFC multi-strand wire called “Silivolt-1V” made by MC/Staubli as its highly flexible & soldering iron resistant. The left cable is the 0.75mm CSA version, & the right being their 2.5mm CSA version. The eye is for a M4 bolt/stud connection.
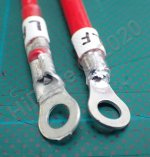
Last edited:
Hello,
No matter how many crimps you need to make you will always need to use a quality tool.
In another thread there are people having problems with soldering ultracaps to a board. In the manual it states you need 80 watts soldering tool.
BUT people will say i only need to make 6 joints so i will try it with a less powerful soldering tool. If it does not work from the start one could buy the right tool but if you think it worked alright but in fact you have a few cold solder joints you will get into trouble sooner or later.
Greetings,Eduard
No matter how many crimps you need to make you will always need to use a quality tool.
In another thread there are people having problems with soldering ultracaps to a board. In the manual it states you need 80 watts soldering tool.
BUT people will say i only need to make 6 joints so i will try it with a less powerful soldering tool. If it does not work from the start one could buy the right tool but if you think it worked alright but in fact you have a few cold solder joints you will get into trouble sooner or later.
Greetings,Eduard
@Mulburg -
With no disrespect to previous posters sharing their experiences. Look to the datasheets and manufacturers specs and guidance and/or truly known and trusted sources of information around the specific connectors you buy.
You posted a picture of one specific type of connector, with one fairly specific question.
You didn't ask, but I would not solder that type of connection, but that's just me. My advice vs. facts - If you want a solder-on type connection, then buy one. I would not use sub-par crimping skills and/or the wrong tools as an excuse to try something that the manufacturer never intended for their product unless you're certain of your outcome and why you're doing it the "wrong" way.
They make connectors of almost every variety in both crimp and solder versions. There may be a few that are intended for both... I'd never say never...
As for the 'article' ... Most importantly... if you're going to get a "ratcheting crimper"... that's an excellent recommendation, IMO. However, it doesn't cover anywhere in the article what specific die they use... I know which one... but did you notice? Using the wrong die leads to pretty crappy crimps.
See below link...
https://www.amazon.com/APIOLO-Crimping-Tool-Set-Non-Insulated/dp/B0C4P4K24H/ref=sr_1_2_sspa?crid=EH91KFOXFRJA&keywords=ratcheting+crimper&qid=1704543063&sprefix=ratcheting+crm,aps,112&sr=8-2-spons&sp_csd=d2lkZ2V0TmFtZT1zcF9hdGY&th=1
Maybe get something like this with an assortment of dies, learn what connectors are appropriate for each die (and vice versa) along with the various sizes. Grab a bunch of spare wire... boxes of pennies worth of connectors to practice with and have a blast! It's a solid investment, IMO.
Again... I love every approach, and I often do it the "wrong" way. Mainly, when I'm in doubt... I trust the manufacturer and try it their way first.
With no disrespect to previous posters sharing their experiences. Look to the datasheets and manufacturers specs and guidance and/or truly known and trusted sources of information around the specific connectors you buy.
You posted a picture of one specific type of connector, with one fairly specific question.
You didn't ask, but I would not solder that type of connection, but that's just me. My advice vs. facts - If you want a solder-on type connection, then buy one. I would not use sub-par crimping skills and/or the wrong tools as an excuse to try something that the manufacturer never intended for their product unless you're certain of your outcome and why you're doing it the "wrong" way.
They make connectors of almost every variety in both crimp and solder versions. There may be a few that are intended for both... I'd never say never...
As for the 'article' ... Most importantly... if you're going to get a "ratcheting crimper"... that's an excellent recommendation, IMO. However, it doesn't cover anywhere in the article what specific die they use... I know which one... but did you notice? Using the wrong die leads to pretty crappy crimps.
See below link...
https://www.amazon.com/APIOLO-Crimping-Tool-Set-Non-Insulated/dp/B0C4P4K24H/ref=sr_1_2_sspa?crid=EH91KFOXFRJA&keywords=ratcheting+crimper&qid=1704543063&sprefix=ratcheting+crm,aps,112&sr=8-2-spons&sp_csd=d2lkZ2V0TmFtZT1zcF9hdGY&th=1
Maybe get something like this with an assortment of dies, learn what connectors are appropriate for each die (and vice versa) along with the various sizes. Grab a bunch of spare wire... boxes of pennies worth of connectors to practice with and have a blast! It's a solid investment, IMO.
Again... I love every approach, and I often do it the "wrong" way. Mainly, when I'm in doubt... I trust the manufacturer and try it their way first.
Hello,
So true !!
If you intend to use a certain terminal check the manufacturer info about which tool to use. You want the termination to keep it " caracteristiques" for a decade at least.
We at Dutch railways are not allowed to use other crimping tools than the ones provided by the company. And we have a specific tool for a specific terminal.
Also not recommended to use crimping and soldering combination.
Greetings Eduard
So true !!
If you intend to use a certain terminal check the manufacturer info about which tool to use. You want the termination to keep it " caracteristiques" for a decade at least.
We at Dutch railways are not allowed to use other crimping tools than the ones provided by the company. And we have a specific tool for a specific terminal.
Also not recommended to use crimping and soldering combination.
Greetings Eduard
I would agree with eduard. Soldering and crimping defeats one of the benefits of crimping. The capillary action in stranded wire wicks the solder up into the bundle creating a stiff and brittle segment that is prone to cracking.
Crimping is supposed to deform the wire bundle and form a very tight (sometimes gas tight) seal and bond and soldering will prevent this from happening.
Most aerospace (my field) and military connectors are crimp types with occasional options for solder. Most of my customers however do not permit soldering. There are exceptions such as coaxial cables and connectors used for backplane connections to a PCB.
As has been mentioned before, every connector type has its own crimp tool with dies for different pin sizes and wire size range. You can go broke buying those things 😂. That is especially true for military connectors DTL-38999 etc.
Crimping is supposed to deform the wire bundle and form a very tight (sometimes gas tight) seal and bond and soldering will prevent this from happening.
Most aerospace (my field) and military connectors are crimp types with occasional options for solder. Most of my customers however do not permit soldering. There are exceptions such as coaxial cables and connectors used for backplane connections to a PCB.
As has been mentioned before, every connector type has its own crimp tool with dies for different pin sizes and wire size range. You can go broke buying those things 😂. That is especially true for military connectors DTL-38999 etc.
Hello,
Soldering before crimping is surely bad. But i know there are people out there who solder after crimping. The idea is the area which is not covered by the crimping will be taken care of by the soldering.
The manufacturing companies surely did do testing to find out the right procedures to get the best results possible so we ( being mostly non professionals) should follow their advice, like we do first using a glue we never used before. But even superglue some people manage to do wrong.
Greetings Eduard
Soldering before crimping is surely bad. But i know there are people out there who solder after crimping. The idea is the area which is not covered by the crimping will be taken care of by the soldering.
The manufacturing companies surely did do testing to find out the right procedures to get the best results possible so we ( being mostly non professionals) should follow their advice, like we do first using a glue we never used before. But even superglue some people manage to do wrong.
Greetings Eduard
If you know how to solder properly the solder doesn't run up the wire past the end of the last "wing" of the crimp.....therefore not a problem of the wire "breaking".
It all depends on the wire & the crimp terminal used....
The OP wire (as shown in their photo) is thin & the crimp terminal type is not suitable for solder & is solely a crimp as its designed that way with close & solid contact between the wire & the terminal...use the correct crimp tool & all should be ok...
In the wire & terminal combinations that I was using (photo in above post) the terminal was the correct size for the wire CSA.....but you never get 100% contact between the terminal & the wire..& I've known the terminal crimp to break some of the strands of thin multi-strand wire...this is why I tin, then crimp & then solder the above type of crimp terminals...100% contact & no chance of some of the strands breaking off..
It all depends on the wire & the crimp terminal used....
The OP wire (as shown in their photo) is thin & the crimp terminal type is not suitable for solder & is solely a crimp as its designed that way with close & solid contact between the wire & the terminal...use the correct crimp tool & all should be ok...
In the wire & terminal combinations that I was using (photo in above post) the terminal was the correct size for the wire CSA.....but you never get 100% contact between the terminal & the wire..& I've known the terminal crimp to break some of the strands of thin multi-strand wire...this is why I tin, then crimp & then solder the above type of crimp terminals...100% contact & no chance of some of the strands breaking off..
"Crimping of solid wire, component leads, or stranded wire that has been solder-tinned, is prohibited."
https://workmanship.nasa.gov/lib/insp/2 books/frameset.html
https://hackaday.com/2016/11/03/specifications-you-should-read-the-nasa-workmanship-standards/
Always use the specified crimp tool for the connectors being used.
If you think the crimp tool is expensive, try costing all the field failures due to poor workmanship.
One failure prevented will pay for the proper crimp tool. And wire "breaking" is a thing.
https://workmanship.nasa.gov/lib/insp/2 books/frameset.html
https://hackaday.com/2016/11/03/specifications-you-should-read-the-nasa-workmanship-standards/
Always use the specified crimp tool for the connectors being used.
If you think the crimp tool is expensive, try costing all the field failures due to poor workmanship.
One failure prevented will pay for the proper crimp tool. And wire "breaking" is a thing.
Hello,
Of course , we do our hobby each person with his own mindset.
But at work i have heard about cables kind of falling out of their terminals just because the project procedure was not taking care of. Usually doing things properly takes more time.
Just had to pee sitting at an outside street restaurant in Vietnam. Ooh toilet is on the right side at the end of this alley where they were cooking.
Greetings Eduard
Of course , we do our hobby each person with his own mindset.
But at work i have heard about cables kind of falling out of their terminals just because the project procedure was not taking care of. Usually doing things properly takes more time.
Just had to pee sitting at an outside street restaurant in Vietnam. Ooh toilet is on the right side at the end of this alley where they were cooking.
Greetings Eduard
Attachments
"Crimping of solid wire, component leads, or stranded wire that has been solder-tinned, is prohibited."
https://workmanship.nasa.gov/lib/insp/2 books/frameset.html
Thats all very well telling people to do stuff to NASA spec, but its a bit OTT when all thats involved is modifying your own personal speakers...
Many general/common crimp terminals (like the ones I used in the my previous photo) break some of the strands in thin multi-strand wires (even when using the correct terminal for the wire gauge & crimp tool)......the only way to stop it is to tin the wire...but that leaves a gap between the wire & the terminal..so then a small amount of solder is added to fill......Yes if you add too much the solder will wick up beyond the last terminal "wing" crimp...so get better with the soldering, it can be done!..
But at work i have heard about cables kind of falling out of their terminals just because the project procedure was not taking care of. Usually doing things properly takes more time.
In my experience, it's usually faster and better to do things properly, so rework is not necessary.
There's no connection more reliable than a gas tight, properly done crimp.
And in the long run, it's cheaper as well.
- Home
- Design & Build
- Construction Tips
- Wire terminal crimping