You can't make it that short.
5khz is 6.8cm long and one quarter wavelength of that is 1.7cm
The wavefront from the back of the tweeter has to travel through the pole piece, which means that even if the metamaterial absorber is really really short, it's still not going to work at 5khz to any significant extent
More importantly, I'd argue the main purpose of the absorber is to reduce the magnitude of the impedance peak. That's down around 500Hz, so there's no real reason to try and make the absorber work at 5khz, it won't be accomplishing anything
I figured this out the hard way when I made an absorber for a planar tweeter and it did absolutely nothing. It literally measured no different than the back cup you get from Parts Express
Realized that it did nothing because there's no impedance peak to dampen.
I'd speculate that it's possible that the "clean" sound of ribbons and planars may be attributable to their lack of impedance peak. If true, then one could "tame" poorly behaved drivers (like compression drivers) with an absorber
Also, I'm really curious if the sealed transmission line works as well. It's much much bigger but certainly easier to calculate and design. Those absorbers that I published and printed were quite a p.i.t.a. to design. Not trying to brag here, but I've been building speakers in 3D for almost ten years now, and those absorbers were a struggle for me. I can make a conventional waveguide in literally ten minutes, I got that down to a science, but those absorbers are gnarly. I had some designs that I abandoned after 20+ hours of sitting glued to the computer.
Years ago, some dude published a cobol script to calculate something comparable, but that's way beyond my skillset
5khz is 6.8cm long and one quarter wavelength of that is 1.7cm
The wavefront from the back of the tweeter has to travel through the pole piece, which means that even if the metamaterial absorber is really really short, it's still not going to work at 5khz to any significant extent
More importantly, I'd argue the main purpose of the absorber is to reduce the magnitude of the impedance peak. That's down around 500Hz, so there's no real reason to try and make the absorber work at 5khz, it won't be accomplishing anything
I figured this out the hard way when I made an absorber for a planar tweeter and it did absolutely nothing. It literally measured no different than the back cup you get from Parts Express
Realized that it did nothing because there's no impedance peak to dampen.
I'd speculate that it's possible that the "clean" sound of ribbons and planars may be attributable to their lack of impedance peak. If true, then one could "tame" poorly behaved drivers (like compression drivers) with an absorber
Also, I'm really curious if the sealed transmission line works as well. It's much much bigger but certainly easier to calculate and design. Those absorbers that I published and printed were quite a p.i.t.a. to design. Not trying to brag here, but I've been building speakers in 3D for almost ten years now, and those absorbers were a struggle for me. I can make a conventional waveguide in literally ten minutes, I got that down to a science, but those absorbers are gnarly. I had some designs that I abandoned after 20+ hours of sitting glued to the computer.
Years ago, some dude published a cobol script to calculate something comparable, but that's way beyond my skillset
This is better:
But if you use dedicated woofer and filter everything above 200Hz then problem is solved?
Berstis lens?Years ago, some dude published a cobol script to calculate something comparable, but that's way beyond my skillset
Evolution creates a metamaterial that absorbs its enemies biosonar: https://phys.org/news/2023-06-moths-invisibility-cloaks-predators-biosonar.html
dave
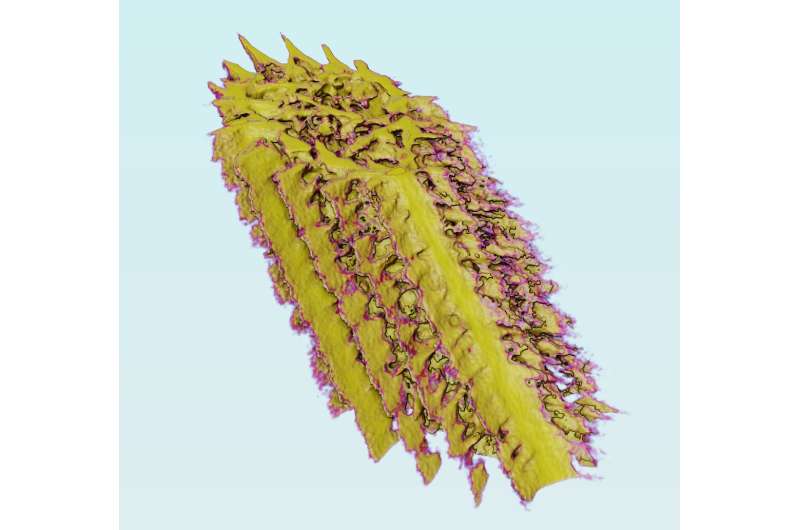
dave
This sounds like an interesting experimentI'd speculate that it's possible that the "clean" sound of ribbons and planars may be attributable to their lack of impedance peak. If true, then one could "tame" poorly behaved drivers (like compression drivers) with an absorber
I figured this out the hard way when I made an absorber for a planar tweeter and it did absolutely nothing. It literally measured no different than the back cup you get from Parts Express
Realized that it did nothing because there's no impedance peak to dampen.
So not even a slight reduction in distortion?
This metamatrial traps light instead of sound:
https://interestingengineering.com/science/light-waves-can-be-frozen-or-trapped-in-3d-materials
dave
https://interestingengineering.com/science/light-waves-can-be-frozen-or-trapped-in-3d-materials
dave
Hi Frank, do you have photos and other info about your version of Hegeman's enclosure??I built an 18.1L enclosure (the same effective volume as Hegeman's enclosure) and tested an H1 woofer in it and in Hegeman's enclosure.
This one seems potentially doable. Plus I think there might be enough info to create their 1 octave example 50-100hz
. Credit https://www.semanticscholar.org/pap...i-Li/47df6d471882ea5efddd4367cc06488eff385ccc
This stuff is certainly quite interesting, but one of the reasons I focused on putting the metamaterial into speakers, instead of putting it onto walls, is that you need to make a LOT of 3D prints to accomplish even a semblance of attenuation.
Even if you could cover 50% of a single wall with 3D metamaterial absorbers, the effect would be little different than opening a window in the room.
I think the technology is fascinating, but the sheer number of units required is daunting and would likely take months to print, running 24x7.
In my old listening room, I bought a bunch of the "bubos" absorbers off of Amazon, and then I basically ratched up their effectiveness by adding a one inch gap behind the absorber.
The idea is similar to the foam in the Geddes speakers:
1) when sound travels through the Bubos absorbers, which are made of felt, you're going to get a little attenuation. The absorbers are about half an inch thick, so you'd expect them to attenuate a few dB but only down to about 6khz or so. (If they were much thicker, they would attenuate more and they would attenuate to a lower frequency.)
2) by adding a gap, a fraction of the sound that radiates THROUGH the absorber should get trapped in the gap between the absorber and the wall behind it. Similar to higher order modes, a fraction of the radiated sound will not go through in a single pass, it will 'see' the acoustic resistance of the absorber and get reflected inside the gap multiple times. Ideally, this should put the reflected wave out of phase with the waves that DO make it through in a single pass. I know that's not a great explanation, but I've tried it both ways, and introducing a gap seems to improve things. Oddly enough, it also seems to look much better. With the absorbers just taped to the bare walls, it looks too much like a recording studio. With the absorbers staggered by an inch, the absorbers seem to 'float' in the air, which looks better. If I really wanted to go crazy, I could put some LED lights behind there.
My friend Jon Whitledge used hundreds of pounds of absorbers in his "Magic Bus." Although that's incredibly labor intensive, the results are really impressive, it's some of the best bass I've ever heard.
Even if you could cover 50% of a single wall with 3D metamaterial absorbers, the effect would be little different than opening a window in the room.
I think the technology is fascinating, but the sheer number of units required is daunting and would likely take months to print, running 24x7.
In my old listening room, I bought a bunch of the "bubos" absorbers off of Amazon, and then I basically ratched up their effectiveness by adding a one inch gap behind the absorber.
The idea is similar to the foam in the Geddes speakers:
1) when sound travels through the Bubos absorbers, which are made of felt, you're going to get a little attenuation. The absorbers are about half an inch thick, so you'd expect them to attenuate a few dB but only down to about 6khz or so. (If they were much thicker, they would attenuate more and they would attenuate to a lower frequency.)
2) by adding a gap, a fraction of the sound that radiates THROUGH the absorber should get trapped in the gap between the absorber and the wall behind it. Similar to higher order modes, a fraction of the radiated sound will not go through in a single pass, it will 'see' the acoustic resistance of the absorber and get reflected inside the gap multiple times. Ideally, this should put the reflected wave out of phase with the waves that DO make it through in a single pass. I know that's not a great explanation, but I've tried it both ways, and introducing a gap seems to improve things. Oddly enough, it also seems to look much better. With the absorbers just taped to the bare walls, it looks too much like a recording studio. With the absorbers staggered by an inch, the absorbers seem to 'float' in the air, which looks better. If I really wanted to go crazy, I could put some LED lights behind there.
My friend Jon Whitledge used hundreds of pounds of absorbers in his "Magic Bus." Although that's incredibly labor intensive, the results are really impressive, it's some of the best bass I've ever heard.
Living in Boeing town allows for cool composites to be found on offerup.
A quick prototype made with kitchen plastic wrap using the esl tensioning method. The honeycomb is 1/4 nomex
The study above used carbon fiber for the rigid material on either side but once I find a cheap to free fire safe material I will try enclosing.
A quick prototype made with kitchen plastic wrap using the esl tensioning method. The honeycomb is 1/4 nomex
The study above used carbon fiber for the rigid material on either side but once I find a cheap to free fire safe material I will try enclosing.
Attachments
- Home
- Loudspeakers
- Multi-Way
- 3D Printed Metamaterials